Anyone thinking about buying a label printer for the first time is often confronted with two different types of product: direct thermal printers (often simply referred to as "thermal printers") and thermal transfer printers. Both direct thermal and thermal transfer printers are used for printing high-quality labels and various printed media. To choose the right label printer, read this article to become familiar with these two printing technologies.
How direct thermal printers and transfer thermal printers work?
Both direct thermal printing and thermal transfer printing use a heated print head to transfer images onto labels.
The main difference is that thermal transfer printing uses a heated ribbon to transfer the ink to the labels, while direct thermal printing uses a special paper coated with chemicals that darken when heated. Neither ribbon nor ink is required for this printing process.
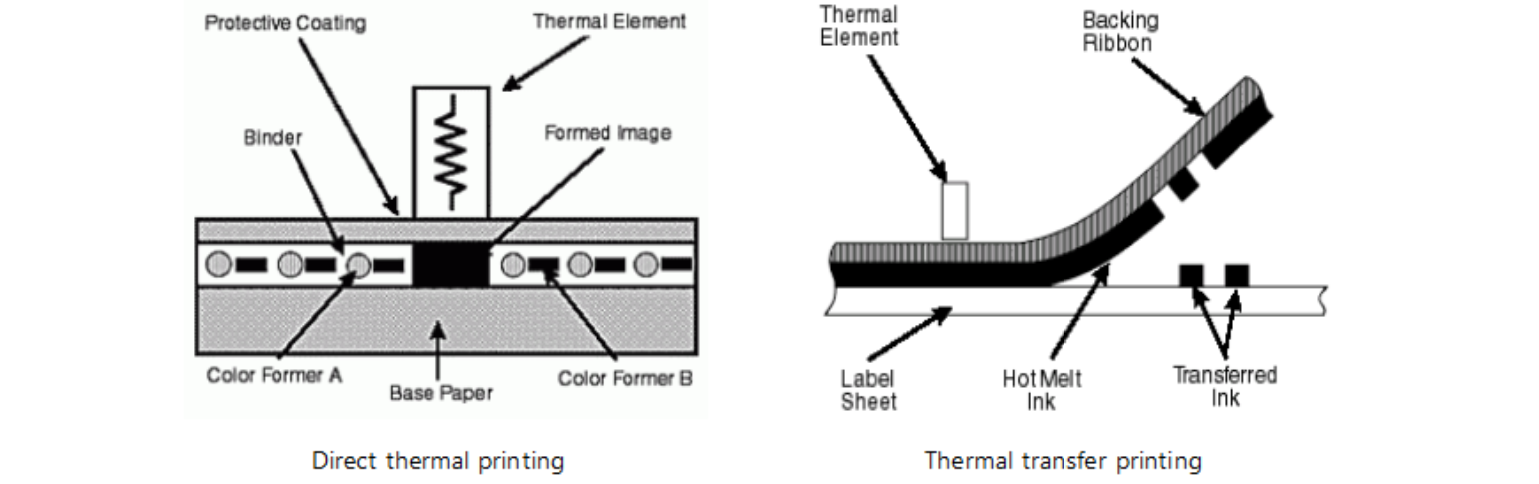
What are the advantages and limitations of direct thermal printing and thermal transfer printing?
Direct thermal and thermal transfer - these two technologies serve similar purposes for different applications. Both technologies have their own additional advantages and disadvantages.
Advantages of direct thermal printing:
- Cost-effectiveness: direct thermal printing is generally more cost-effective as no ink, toner or ribbons are required.
- No ink, toner, ribbons: without ink, toner or ribbons, direct thermal printing simplifies the printing process and reduces maintenance.
- Easy to use:direct thermal printers are also accessible to non-technical users. They are generally easy to set up and have simple interfaces.
- Quick and efficient printing: direct thermal printers can print large quantities in a short time.
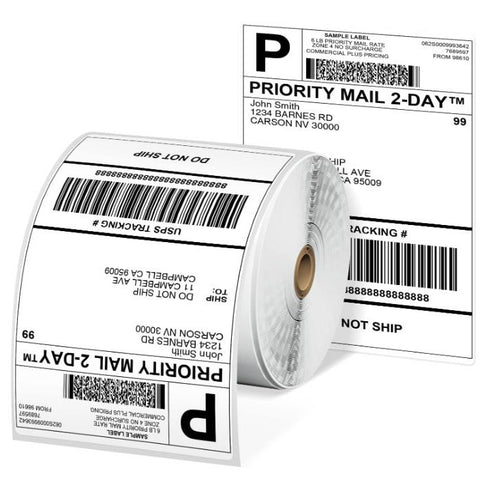
Advantages of thermal transfer printing:
- Color printing:a major advantage of thermal transfer printing is the ability to use ribbons to produce colorful labels, making it suitable for applications that require an eye-catching appearance.
- Extremely scratch resistant :thermal Transfer labels are extremely durable and scratch resistant, ensuring that printed information remains legible even in demanding environments.
- High-durability:thermal transfer labels are designed to withstand sunlight, extreme temperatures and harsh environmental conditions, making them suitable for indoor and outdoor use.
- Not fades easily: thermal transfer printing produces durable, fade-resistant prints that ensure labels and tags maintain their clarity and legibility over time.
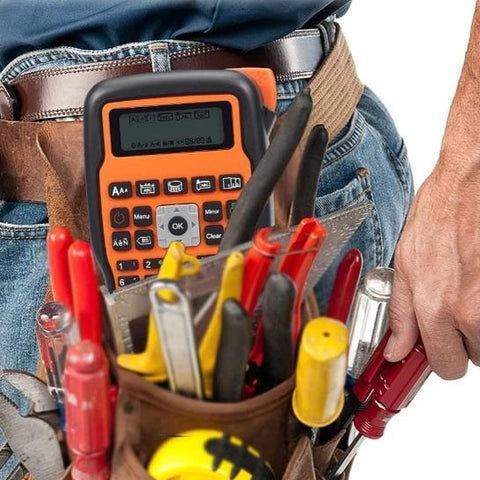
Limitations of direct thermal printing:
- No color printing:direct thermal printing is limited to monochrome or black-and-white options.
- Lack durability:direct thermal printing can fade over time and has a shorter lifespan compared to thermal transfer printing.
- Limited applications: direct thermal labels are sensitive when exposed to heat, sunlight or other harsh conditions.
Limitations of thermal transfer printing:
- Ribbons are necessary: thermal transfer printing requires ribbons, which increases the overall cost.
- Ribbon replacement: setting up and changing the ribbon requires additional time.
- Print speed: thermal transfer printing tends to be slower compared to direct thermal printing, which affects overall efficiency.
Which kind of thermal printer should I choose?
For short-term applications, direct thermal printers are an ideal choice. These printers do not require ink or ribbons, which are not only easy to use but also offer a wide range of customized patterns. Direct thermal labels are widely used in areas such as:
- Shipping labels: efficient tracking and identification of parcels in shipping and logistics processes.
- Labels for temporary products: such as food labels, providing temporary labeling solutions for fast-moving products.
- Price labels: facilitates fast and accurate price labeling of goods.
- Name tags: create personalized name badges for events, conferences or workplaces to improve identification and organization.
- Other applications: barcode labels, tickets, receipts and much more.
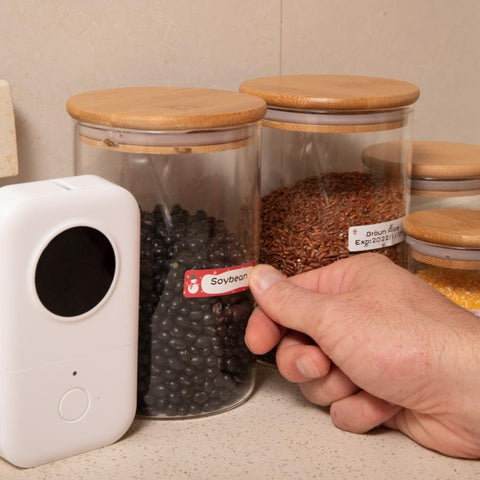
For long-term applications, thermal transfer printer is a good choice. Thermal transfer labels can withstand harsh conditions such as chemicals, heat, oil or water. Here are some of the most common uses of thermal transfer labels:
- Wire and cables: thermal transfer labels are ideal for the clear and permanent marking of cables and wires, even in harsh environments.
- Asset tracking: thermal transfer labels offer a long shelf life and allow assets to be accurately tracked throughout their lifecycle.
- Laboratory: thermal transfer labels can withstand chemicals, solvents and extreme temperatures.
- Outdoor usage: labels are exposed to sunlight, moisture and harsh weather conditions. Thermal transfer labels are preferred because they maintain their legibility and durability over time.
- Other applications: thermal transfer labels are also used in various other areas such as manufacturing, logistics, healthcare and retail where durable labeling is essential for inventory management, product identification and regulatory compliance.
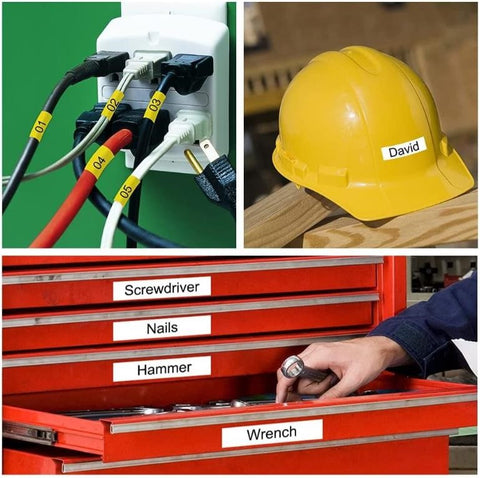
Need more?
After reading this article, if you're not sure which specific product from Phomemo is right for you, just leave a comment below. We will recommend the best product for your needs. Phomemo is always here and ready to assist you!